When BETCO, Inc., of Statesville, N.C., decided to add a roll-up door line, they discovered a better packaging method in the process. The company, which manufactures self-storage buildings and general-purpose buildings, began producing roll-up doors for their self-storage buildings in August 2000 and has since begun selling them to other companies.
Because the roll-up door line was new for BETCO, the company needed to find a way to package the doors for shipment. The packaging had to work on a flatbed trailer so that the roll-up doors could be shipped with the rest of BETCO’s products. Other door suppliers were using metal banding and lattice structures made from nailed-together lumber for packaging and shipping. But BETCO wanted to find an easier, more economical method and improve on the industry standard.
While searching for a solution, Joe Rabon, BETCO’s purchasing manager at the time, discovered Rollguard products on the Internet. “The initial idea was to use foam roll cradles as a cushion between the doors,” BETCO’s current purchasing manager, Neely Cunningham, C.P.M., said. However, Rollguard Products recommended their Recycled Fiber roll cradles instead.
“Recycled Fiber was more economical for BETCO’s application and would hold up well against their products,” Rollguard Products’ sales manager, Rob Swannell, said.
BETCO uses Rollguard’s Recycled Fiber FS-13-1/2 roll cradles. They feature a three-roll configuration, are 44 inches long to precisely fit the width of BETCO’s pallets and come shipped in hinged pairs.
The cradles are separated and set widthwise on the pallet to hold the first layer of three doors in place. Additional cradles are then folded back-to-back along their hinges to create two-sided cradles that enable the stacking of the second through fifth layers of doors. More cradles are then separated and laid upon the top layer of doors to hold the fifth and final layer in place, and the entire load is then stretch wrapped vertically. By stacking five layers high, BETCO is able to ship 15 doors per pallet.
To ensure maximum stability in stacking this high, Rollguard recommended and made some slight design modifications to its cradle. “We found that the roll-up self-storage doors are not perfectly cylindrical like a roll of plastic film,” Swannell said. “Because of the thickness of the door, there’s a defined end to the roll that makes it out of round which created some challenges. We designed some additional spacing to make the cradles higher and wider. We also added some thickness to accommodate the heavier product.”
The greater thickness of the hinged cradles led to an additional challenge. “We use a hoist to load our doors on the pallet,” Cunningham said. “When we folded a cradle and set it down on top of the previous row to start another row, there was too much memory in the hinge, and it would unfold before we could get the next door swung over with the hoist. So we either needed an extra person to hold it down, or we had to tape it in place until we could bring another door over which meant we lost productivity. Rollguard added a bigger perforation in the hinge, and that solved the problem.”
“They have been very responsive to our needs and requirements,” Cunningham continued. “We had to find a way to maximize the number of doors on a pallet that would ensure safety in handling and protection of the roll-up doors during shipment. There were several concepts thought of in the process, but this was the best solution.”
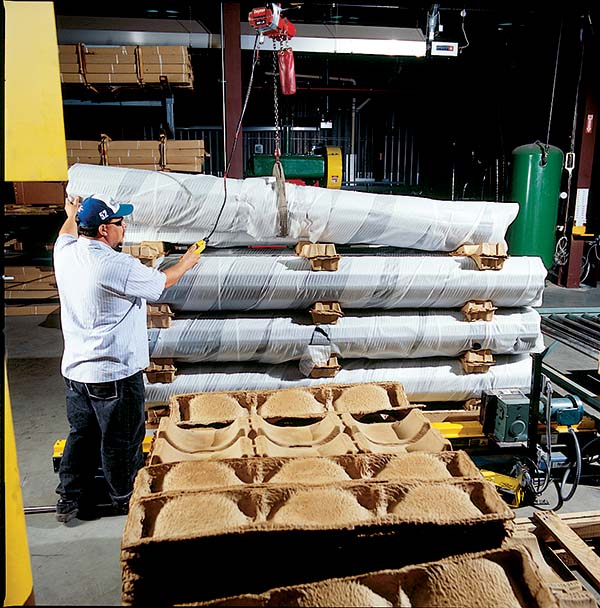