Fiber Roll Cradles Deliver Savings, Performance, Environmental Solutions
Sustainable packaging means reducing the number of components and using recycled and recyclable materials.
MACtac, a world leader in the manufacture of pressure-sensitive adhesive paper, recently teamed up with Rollguard®, part of Great Northern Corporation, to implement a new approach that not only achieves sustainability but also delivers labor and materials savings and improves worker safety — all the while enhancing product protection.
MACtac, a Bemis company, produces Pressure Sensitive Adhesive jumbo rolls and ships them to their finishing centers located around the country. The finishing centers slit the product into widths of 2 inches to 20-plus inches and wind them into lengths of 3,000 to 20,000 feet. The rolls are then shipped to MACtac customers who further convert them into end-customer
products such as bottle labels for wine, mustard, shampoo and other consumer products.
“Our finishing centers previously utilized a multi-part package with a total of eight discrete components,” said Dave DeSimio, Supply Chain Director for MACtac North America, which is headquartered in Stow, Ohio. “With Rollguard, we have been able to reduce that to five components.”
“Our shipping components used to include a pallet, chipboard, foam sheet, foam wedges, poly strapping, a poly cover sheet, a corner board through the cores of multiple rolls to stabilize the load, and finally stretch film to protect the product and to help further stabilize the rolls,” DeSimio explained. “Now we just use a pallet, a Rollguard recycled fiber cradle, poly strapping, a poly cover sheet and stretch wrap.”
DeSimio contacted Rollguard last spring after one of his engineers brought him a trade magazine article about a converter that was having shipping success using Recycled Fiber Full Roll Cradles from Rollguard®, which is headquartered with Great Northern Corporation in Appleton, Wisconsin. “I thought this was obviously an opportunity for us to gain internal and external savings for our customers, and not just monetary savings.”
DeSimio went to the Rollguard Web site and contacted the company. Account Manager John Laura answered the call and soon, joined by General Manager Rob Swannell, Rollguard was investigating MACtac’s needs.
“I had three primary hurdles we were trying to overcome and I gave them to Great Northern when I first made contact with them,” DeSimio said. “One was ergonomics or safety. The second was throughput or lean; we wanted simplification of the packaging structure. The third was green. We are on board with the green initiative through our new packaging.”
“The new Rollguard product accomplishes all three of these,” DeSimio added.
- Better ergonomics has resulted from fewer packaging components. “By only having to put down one item on the skid before the product is placed down versus putting down two or three items, we’ve reduced the number of hazardous body positions per skid,” he said.
- Throughput or lean was improved by reducing the components from eight to five. “We simply place the roll cradle down, place the product on the cradle, finish our packaging and the load is ready for shipment.”
- Sustainability improvement was achieved in several ways. “Getting more green came from getting rid of the foam sheet, getting rid of the Styrofoam wedges and significantly reducing our stretch wrap — all of those being petroleum-based products. Those are all removed or significantly reduced and replaced by a single recycled and recyclable product,” DeSimio said.
Less stretch wrap also is a tribute to the increased performance delivered by the fiber cradles.
“Before, when we were using individual wedges, we used a higher quantity of stretch wrap to ensure that the load didn’t shift, even if the wedges came loose from the roll,” DeSimio said. “The load is more stable now with the roll cradles so we need considerably less poly wrap to ensure stability.”
Rollguard’s fiber roll cradles come in a variety of configurations, all of which are made with recycled corrugated molded pulp and are 100 percent recyclable.
The full-roll cradles are made to provide support along the entire length of cylindrically shaped products and are ideal for heavy rolls with diameters from 9 to 40 inches.
The standard full roll cradles measure 37 inches wide by 47 inches long with a deep well created by 5.5 inches in wall height.
The recycled fiber roll cradles also are available in other configurations for rolls of 3 to 45 inches and a narrow version for rolls of 4 to 11 inches in diameter.
“John (Laura) and Rob (Swannell) visited multiple sites for MACtac,” DeSimio said. “We started off with their standard full roll fiber cradle products and then did a gap analysis to see if their standard products would meet all of our needs,” he said. “They ended up creating a new perforated roll cradle for us.”
The new product, which is called the Recycled Fiber Full Roll Perfed roll cradle, has perforations at 20 and 40 inches in length that greatly expand the pallet size options. When combined with Rollguard’s standard fiber cradle lengths, the following pallet sizes (in inches) now can be accommodated: 30×30, 36×36, 45×45, 48×30, 48×40, 48×48, 54×30, and 60×30.
The new perforated cradle not only makes it quicker and easier to create multiple pallet configurations, it also increases the safety of the process.
“The only reason the new product is perforated, for MACtac at least, is safety.” DeSimio said. “Now our employees, in order to trim the cradle to fit multiple pallets, don’t have to use a knife, so we have significantly reduced the possibility of cutting injuries or lacerations.”
MACtac began testing the new perforated roll cradle product in mid-July and now uses it at four of its eight finishing centers with plans to expand its use to all eight centers by Jan. 1, 2009.
The response has been positive across the board, DeSimio said. “In our internal ergonomic assessments, we’ve seen significant improvements by reducing hazardous postures with high frequency and durations,” he said.
“We have had the cradles in four of our eight centers since July 14 and we have had zero freight claims on our rolls up to 10,000 feet in length,” DeSimio said. “The performance has been at least as good if not better than the eight-component structure. The single cradle provides superior roll stabilization.”
Teaming up with Rollguard has been a winning decision for MACtac on multiple levels.
“The Rollguard cradles provide a substantial cost savings in direct materials and labor to both MACtac and our customers,” said DeSimio.
He added that working with John Laura and Rob Swannell has been a very positive experience.
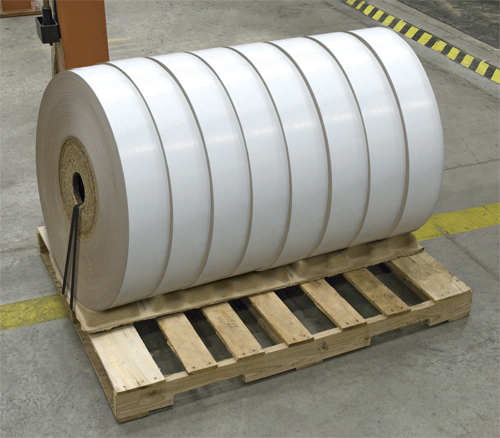